Von Florian Weigmann, Chief Product Officer der PlusServer GmbH
Die Art und Weise wie produziert und gearbeitet wird, ändert sich durch die Digitalisierung grundlegend. Das Stichwort “Industrie 4.0” fungiert in diesem Kontext als Oberbegriff für die moderne, automatisierte Fabrik (Smart Factory) und die damit verbundene vernetzte Produktion. In einer digitalisierten Fertigung sind Maschinen, Menschen und Produkte miteinander verbunden und befinden sich im kontinuierlichen Informationsaustausch. Die smarte Fertigung bietet Unternehmen eine Vielzahl an Möglichkeiten, das eigene Geschäftsmodell zu erweitern oder gänzlich auf den Prüfstand zu stellen. Datenbasierte Geschäftsmodelle, Losgröße 1 oder eine selbststeuernde Produktion sind nur ein kleiner Ausschnitt. Doch von heute auf morgen lässt sich eine intelligente Fertigung nicht realisieren. Es ist ratsam vier grundlegenden Schritten zu befolgen.
1. Analyse und Vernetzung
Um die Systeme miteinander zu vernetzen, müssen nicht unbedingt neue Anlagen erworben werden. Im Vorfeld des Umstiegs auf eine smarte Produktion können in den meisten Fällen die bestehenden Systeme und Maschinen unter Zuhilfenahme von IoT-Technologien verbunden werden, um so einen Retrofit zu ermöglichen. Entsprechend installierte Sensoren können dann Temperaturen, Stromaufnahme, Vibrationsanalyse oder ähnlichen Parameter der Maschinen erfassen. Ergänzend gibt es Module, die diese Daten sammeln und entsprechend an eine IoT-Plattform weiterleiten. Dies geschieht entweder durch eine integrierte Sim-Karte, das lokale WLAN oder über ein kabelgebundenes Ethernet. Um alle Daten der angeschlossenen Geräte zu aggregieren, gibt es in den Fabrikhallen oder auf dem Werksgelände zwischen Maschinen und Netz ein Edge-Device. Mit diesen Edge-Servern lassen sich die Daten auch vorverarbeiten. So wird es möglich, Bandbreite als auch Speicherplatz einzusparen. Die tatsächliche Hardware-Installation ist dabei abhängig von den konkreten und individuellen Anforderungen. Eine ausführliche Planung und vorherige Analyse des Bedarfs sind unumgänglich.
2. Prozess-Transparenz
Um eine einheitliche Kommunikation zwischen Sensoren über Gateways bis hin zu den verarbeitenden IT-Systemen im Backend oder in der Cloud zu gewährleisten, geschieht der Datenaustausch meist über ein spezielles Kommunikationsprotokoll wie OPC-UA (Protocol for Communication Unified Architecture).
Unternehmen erfassen damit eine Vielzahl sehr unterschiedlicher Daten. Beispielsweise Parameter wie Feuchtigkeit, Temperatur, Geschwindigkeit, Druck, Drehmoment oder Auslastung. Neben diesen maschinenabhängigen Daten fließen noch eine Reihe weiterer Daten mit ein, beispielsweise zu Industriesteuerungen oder aus einer ERP-Anwendung (Enterprise Resource Planning). Diese werden ebenso wie die Maschinendaten in einer Cloud-Plattform gesammelt. Aufgrund der sehr unterschiedlich erfassten Daten ist es wichtig, nur die jeweils zum Anwendungsszenario passenden Daten auszuwählen. Durch eine visualisierte Aufbereitung (als digitalen Zwilling) in einem Dashboard wird darüber hinaus Klarheit über die eigenen Prozesse geschaffen. So kann die physische Welt 1:1 in einer virtuellen Fabrik abgebildet werden und bietet Echtzeit-Einblicke in die Fertigung. Darüber hinaus lassen sich Veränderungen an Prozessen simuliert werden. Diese können nach einer erfolgreichen virtuellen Implementation in die reale Welt übertragen werden.
3. Automatisierung und Optimierung
Die gesammelten Daten und die Transparenz der eigenen Prozessschritte bieten die Basis für die Automatisierung bzw. Optimierung von Fertigungs- und Serviceprozessen. Durch eine Echtzeit-Analyse lassen sich die Prozesse deutlich verbessern. Die erlangte Transparenz über Ineffizienzen im Prozess können dazu beitragen, die Produktivität des Fertigungsprozesses deutlich zu erhöhen. Wenn die IoT-Plattform ergänzend mit dem MES (Manufacturing Execution System) oder der Produktionssteuerung verbunden ist, ist die Fertigungsoptimierung besonders wirkungsvoll. Einige Beispiele:
Predictive Maintenance
Die vorausschauende Wartung oder Instandhaltung ist wohl eines der bekanntesten Einsatzszenarien. Da Maschinendaten häufig ganz individuell vom Alter und vom Abnutzungsgrad abhängig sind, kann eine genaue Auswertung der Daten dazu beitragen, Abweichungen oder Fehlermuster zu erkennen.
Dadurch können Verschleiß oder sich entwickelnde Störungen frühzeitig erkannt werden, dies gibt dem Wartungsservice genügend Zeit, angemessen zu reagieren. Dadurch können nicht nur ungeplante Ausfälle vermieden werden, auch Ersatzteile werden erst dann verbaut, wenn diese wirklich notwendig sind.
Lastspitzenmanagement
Lastspitzen sind in der Regel teurer als die Grundlast. Für einen kosteneffizienten Betrieb, sollte das Stromnetz also relativ gleichmäßig belastet werden. Mit Hilfe des IoT können Unternehmen ihren Energieverbrauch bis auf die kleinste Ebene, sprich einzelne Geräte, überwachen und bei drohenden Lastspitzen einzelne Verbraucher abschalten. Dieser Prozess kann in einer Cloud-Plattform sogar automatisiert werden.
Individualisierte Produktion mit Losgröße 1
Die Herstellung von individuellen Einzelstücken (Losgröße 1) gehört auch in größeren Industrieunternehmen längst zum Alltag. Eines der besten Beispiele ist wohl die personalisierte Fertigung von Automodellen. Mit einer ausgereiften Smart Factory können die Produktionszeiten als auch die Extrakosten für solche individuellen Anfertigungen geringgehalten werden.
4. Smart Services
Datenbasierte Dienstleistungen (Smart Services), welche auf individuellen Anforderungen von Kunden basieren, gehören aktuell noch zu den größten Herausforderungen in Bezug auf Smart Factories. Diese Entwicklung markiert einen Wendepunkt vom Verkauf von Maschinenleistung hin zum Verkauf individueller Lösungen.
So können mit Zusatzdiensten wie Wartung, Echtzeitüberwachung oder Prozessoptimierung langfristige Kundenbeziehung aufgebaut und „Equipment as a Service“ ermöglicht werden. In diesem Modell mieten Unternehmen die Maschinen (mit verbrauchsbasierter Abrechnung) und der Anbieter übernimmt Wartung, Reparatur sowie die Lieferung von Ersatzteilen oder Verbrauchsmaterialien.
Der Aufbau einer digitalisierten Produktion bringt eine Vielzahl an Vorteilen mit sich: sinkende Produktionskosten, optimierte und reibungslose Prozesse und eine leicht an sich verändernde Bedingungen anpassbare Fertigung. Wer auf die Smart Factory setzt, kann sich als Unternehmen deutliche Vorteile gegenüber Mitbewerbern verschaffen.
Mehr zum Thema „Smart Factory“ erfahren Sie in unserer Webinar-Aufzeichnung „IIoT und die Cloud – Nichts geht ohne den Digitalen Zwilling!“ – Ein Gespräch zwischen Florian Weigmann (PlusServer GmbH) und Lukas Lutz (GFT Technologies), verfügbar in unserem members+Bereich.
Über den Autor:
Florian Weigmann ist seit Mai 2019 Chief Product Officer der PlusServer GmbH. Sein besonderes Augenmerk liegt dabei auf den Bereichen Datenarchitektur und Datensicherheit innerhalb skalierbarer Cloud-Infrastrukturen. Weigmann verfügt über große Erfahrung im B2B- und B2C-Produktmanagment sowie der Produktentwicklung von Maschinenbau bis Business-Software.
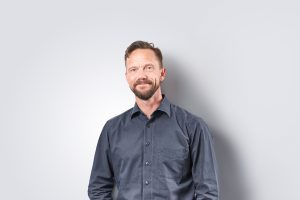